Machining Polycarbonate | CNC Machining and Polycarbonate Parts
Polycarbonate has high impact strength and optical clarity — it’s a versatile thermoplastic that is ideal for safety equipment, electronic components, and more.
At Yijin Hardware, our ISO 9001 certified factory specializes in CNC machining services for polycarbonate parts, ensuring precision, quality, and fast turnaround times for every project.
- ⬤Service
- ⬤Your Details
- ⬤Submit
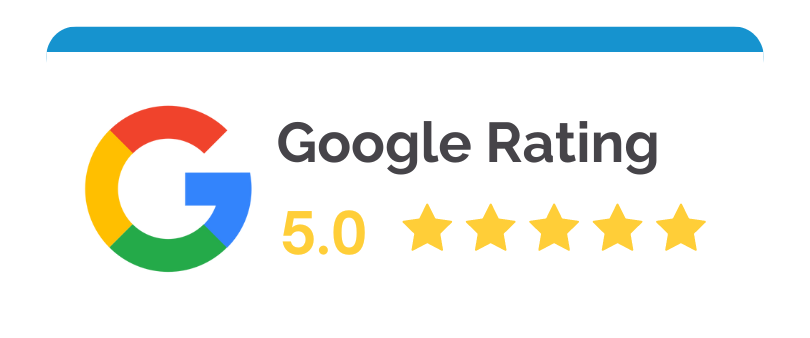
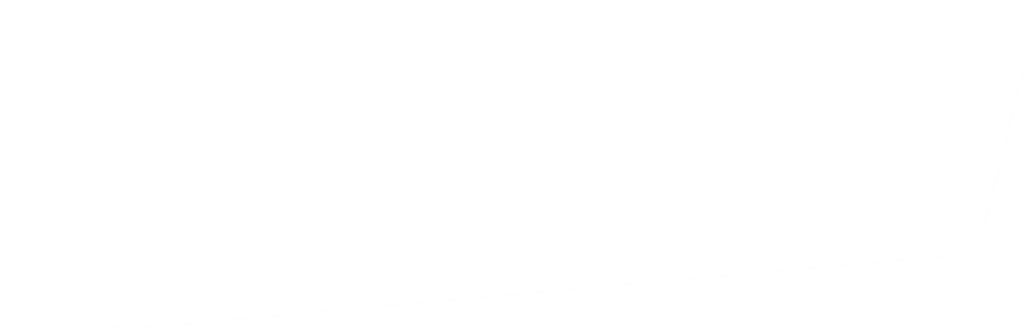
What is CNC Polycarbonate Machining?
CNC polycarbonate machining uses computer-controlled machines to shape and cut polycarbonate material into specific parts or components. This method allows for high precision and repeatability, making it suitable for both small-scale prototypes and large production runs.
The CNC machining process includes various techniques, such as milling, turning, and drilling, tailored to the specific needs of the project.
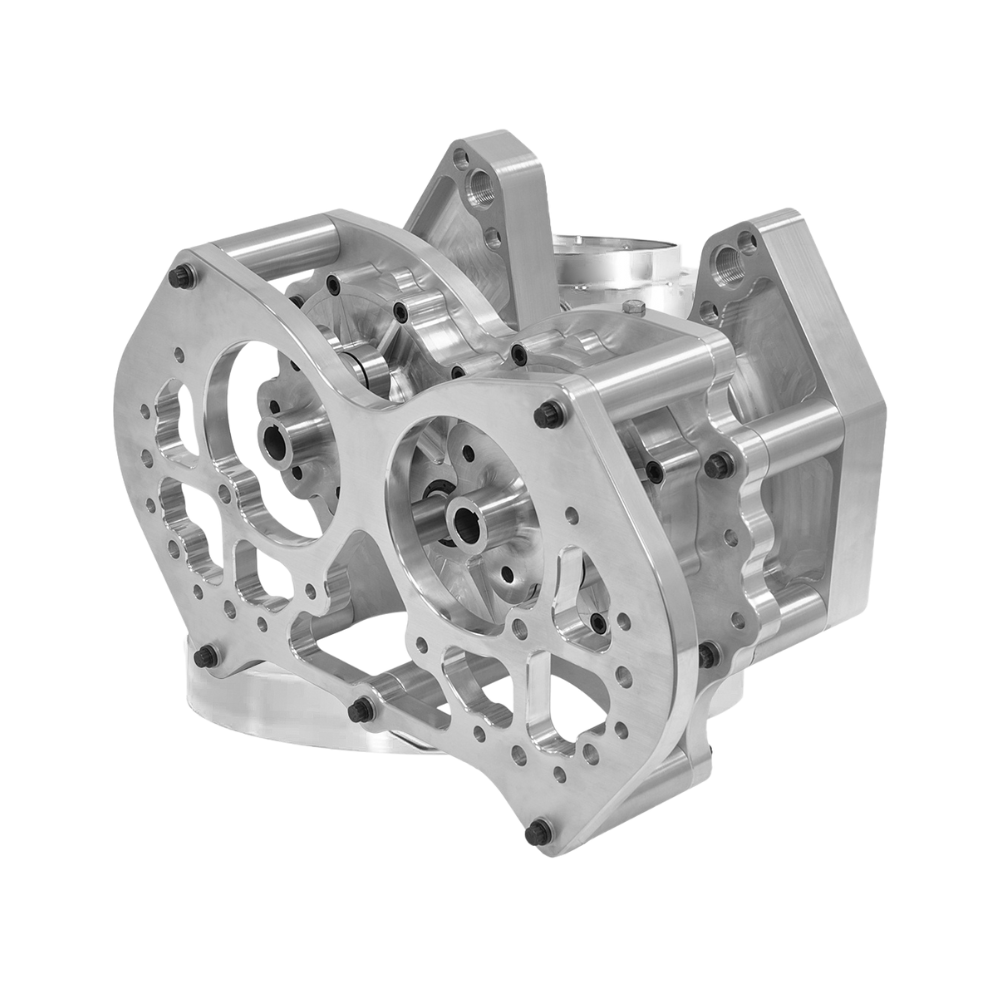
Milling
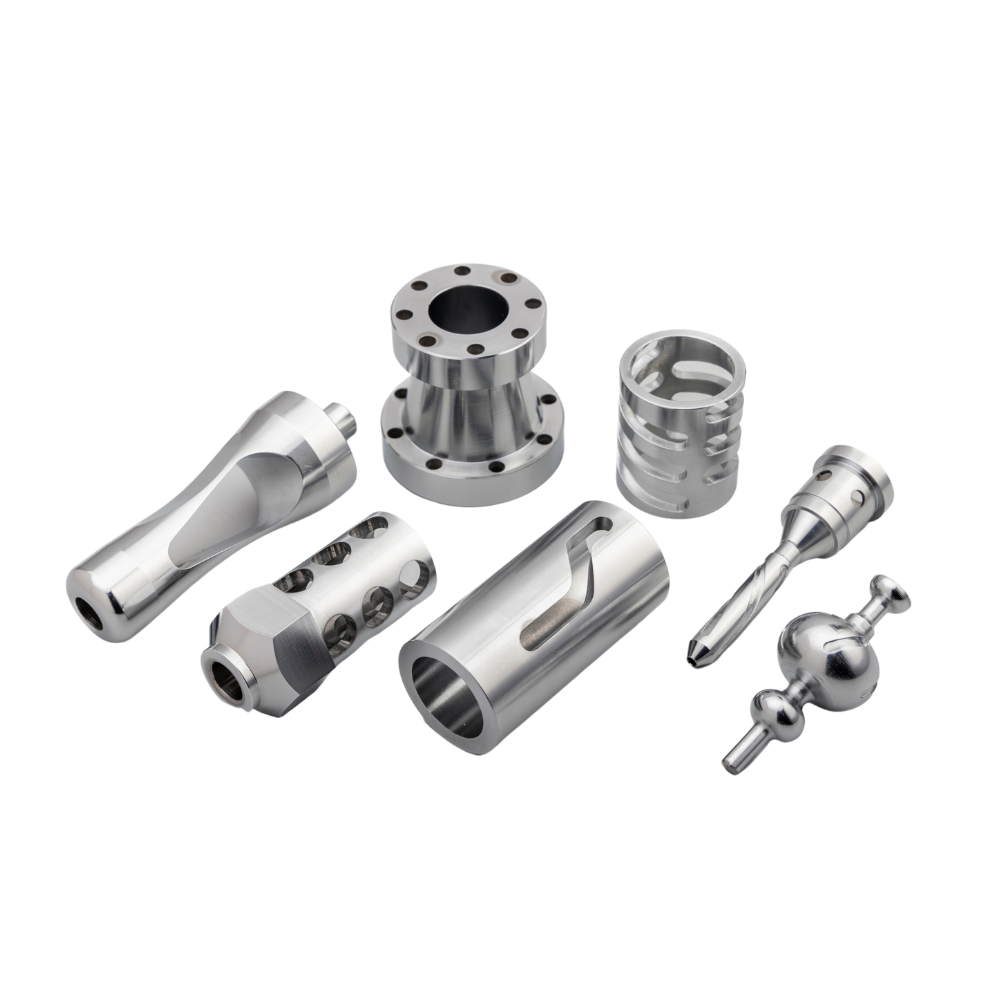
Turning
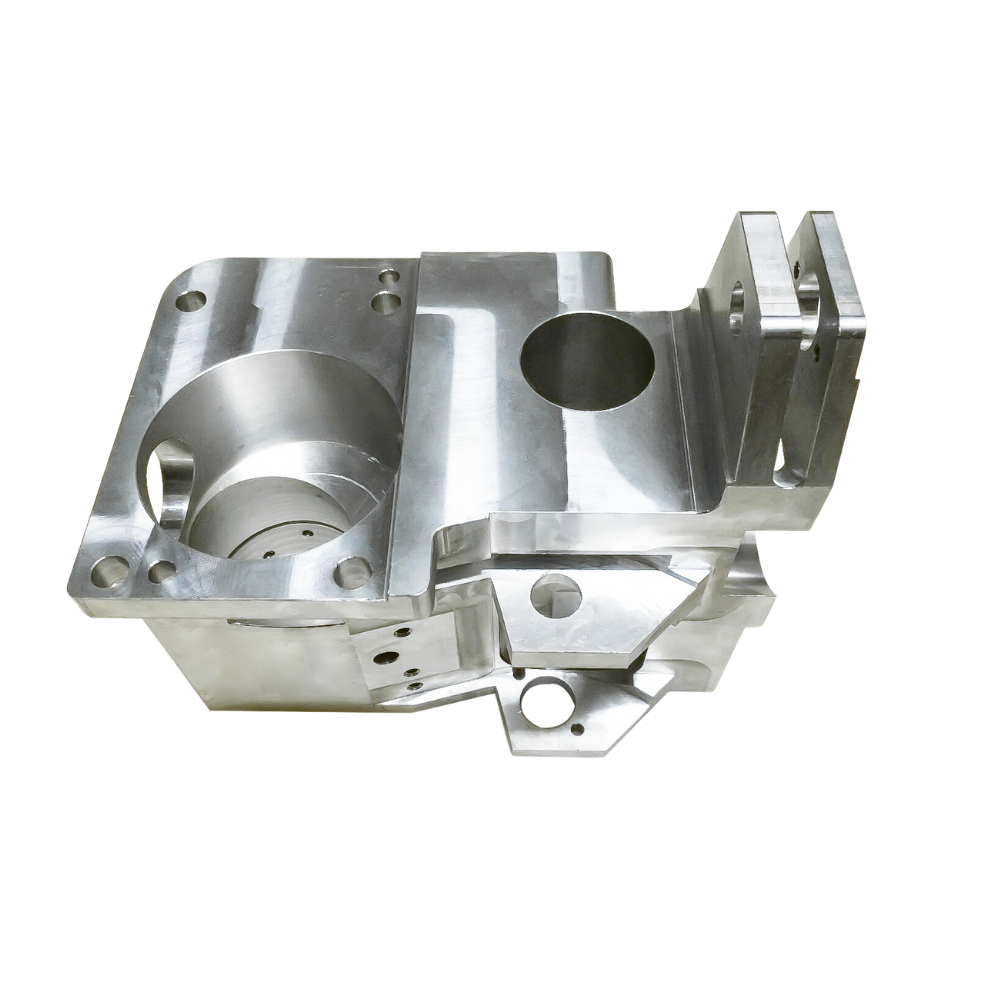
Drilling
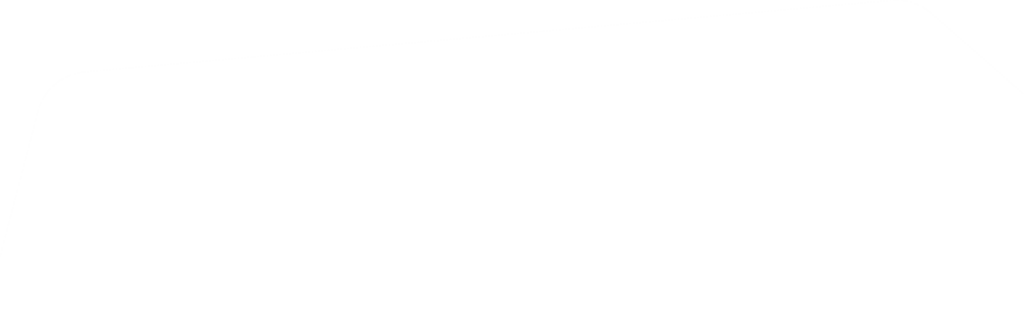
Generic PC (Polycarbonate)
Generic polycarbonate (PC) is an amorphous thermoplastic known for its durability and versatility. It is widely used in industries ranging from automotive to electronics due to its excellent mechanical properties.
Polycarbonate is often chosen over other plastics like acrylic due to its stronger impact resistance and optical clarity. This makes it an ideal material for applications requiring both strength and transparency.
Generic PC Properties
Key polycarbonate properties include impact strength, optical clarity, tensile strength, dimensional stability, chemical resistance, and UV resistance.
Property | Description |
---|---|
Impact Strength | High resistance to impact; less likely to chip or break |
Optical Clarity | Excellent transparency; comparable to glass with a refractive index of 1.548 |
Tensile Strength | Strong resistance against stretching or pulling forces |
Dimensional Stability | Maintains shape under varying temperatures and conditions |
Chemical Resistance | Good resistance to solvents and chemicals; reduces risk of stress cracking |
UV Resistance | Protects against degradation from UV exposure; suitable for outdoor applications |

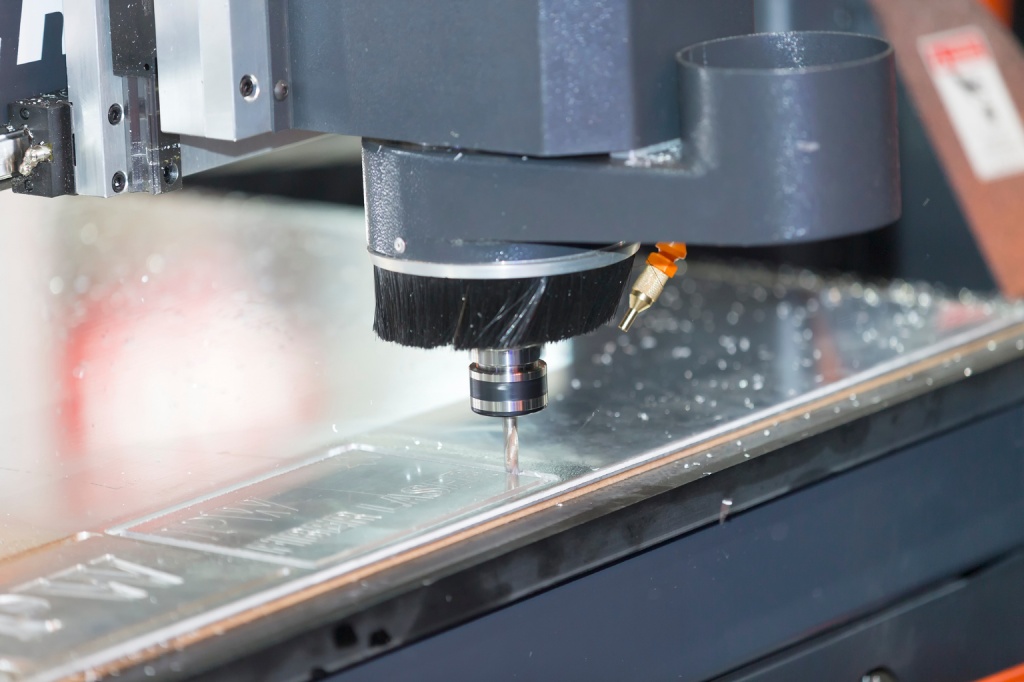
Polycarbonate CNC Finishes
Finishes include as-machined, vapor polishing, bead blasting, painting, laser engraving, and anodizing:
- As-Machined Finish describes the surface directly after machining; it may have tool marks.
- Vapor Polishing is a method that enhances clarity by smoothing the surface using vaporized solvents.
- Bead Blasting provides a matte finish while removing minor imperfections.
- Painting adds color or protective coatings to enhance aesthetics and durability.
- Laser Engraving creates detailed markings or designs on the surface.
- Anodizing increases corrosion resistance and can improve appearance.
Our Design Guide: How to Save Money
- Subassemblies: Design parts that can be combined into subassemblies to minimize the assembly time for your CNC machining project
- Uniform Features: Use consistent features across multiple parts to streamline production
- Simplified Geometry: Avoid complex shapes that require extensive machining time
- Standard Sizes: Use standard dimensions where possible to reduce material waste
- Material Selection: Choose the appropriate grade of polycarbonate based on application needs; higher grades may be more costly but offer better performance
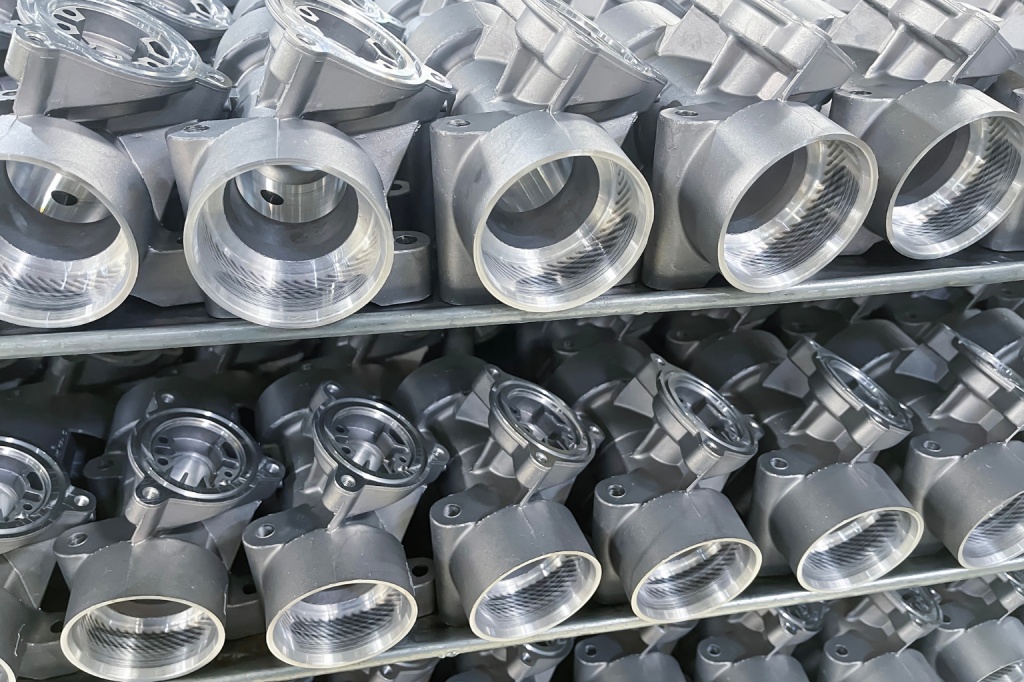
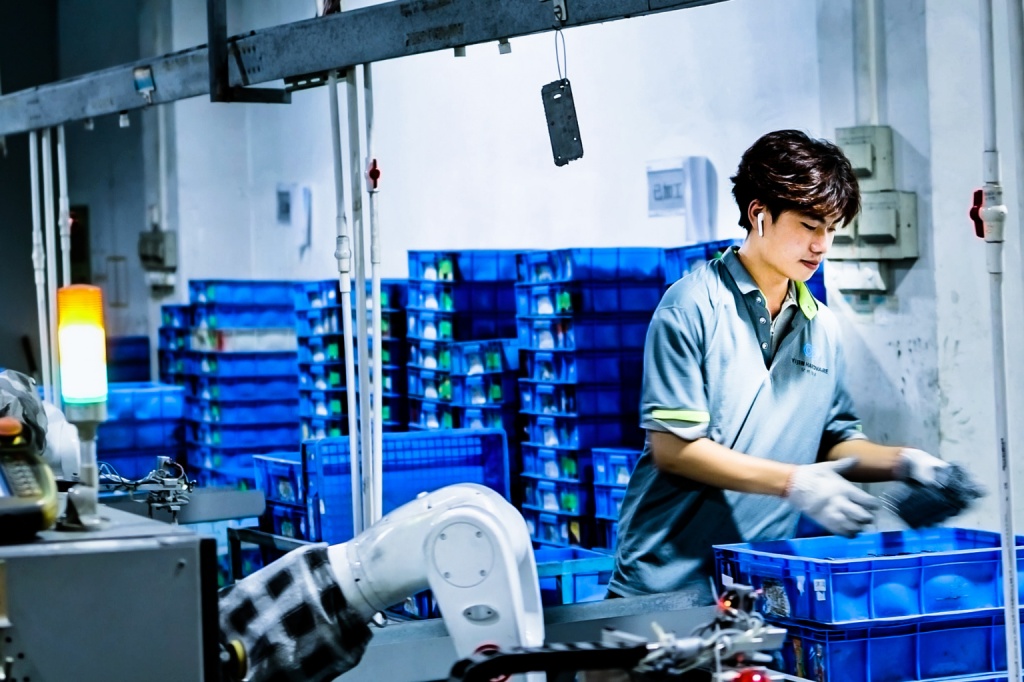
Our CNC Machining Polycarbonate Services
Yijin Hardware uses innovative multi-axis CNC machines to provide our clients with high-quality polycarbonate machined parts. From prototyping materials to high-volume production, we ensure every part that leaves the factory is precisely built to your specifications.
Our turnaround times:
- Urgent High-Precision Sample: Within 24 hours
- New Mold Requirement: Production within 5 days and delivery within 7 days
- Standard Prototyping: Between 5 and 7 days
- High-Volume Production: Usually 2 to 4 weeks, depending on the project’s specifications
Why Choose Yijin Hardware for Machined Polycarbonate Parts?
At Yijin Hardware, we provide affordable CNC machining services tailored specifically for polycarbonate parts. Our premium CNC technology ensures we produce high-quality machined polycarbonate components with excellent dimensional stability and surface finishes. We serve various industries including:
- Automotive
- Aerospace
- Medical devices
- Consumer electronics
With our expertise in polycarbonate CNC machining, we deliver custom polycarbonate parts that meet your exact specifications while maintaining competitive pricing.
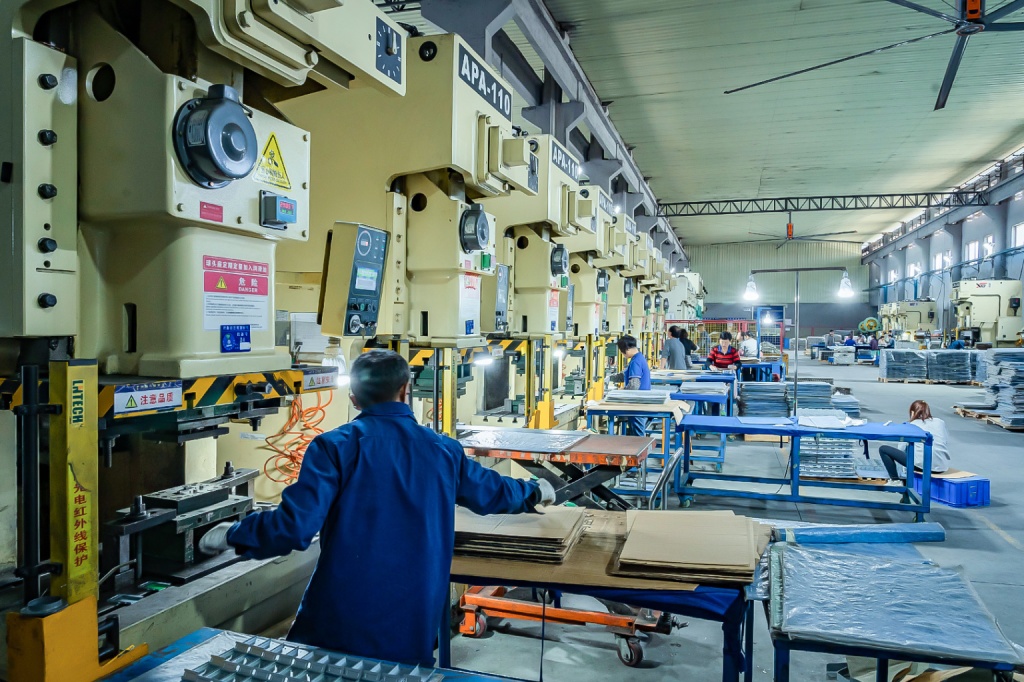
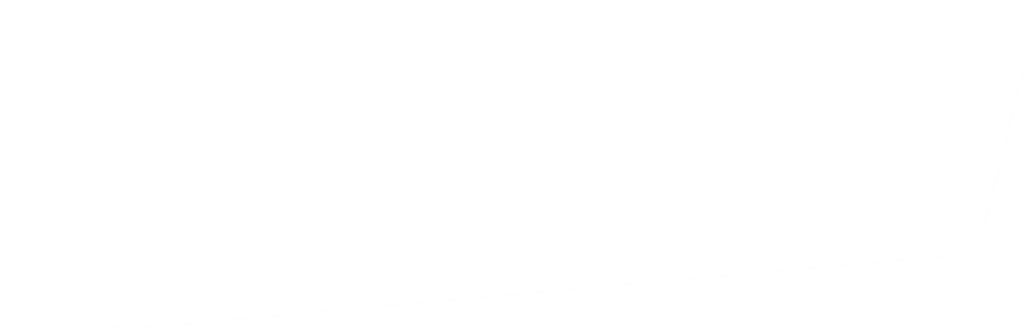
Machining Polycarbonate | CNC Machining and Polycarbonate Parts FAQs
Machining polycarbonate involves processes like CNC milling and CNC turning, which leverage its good machinability and high toughness. Polycarbonate plastic can be shaped into optically clear and precise polycarbonate machined parts, making it ideal for engineering plastic applications requiring excellent impact strength. When using polycarbonate for plastic parts, cutting tools must be sharp and properly maintained to avoid surface damage during plastic sheet machining.
Polycarbonate processing methods include CNC machining in polycarbonate, which produces highly detailed CNC machined polycarbonate parts, and injection molding for mass production. These techniques take advantage of the properties of polycarbonate, such as its high modulus of elasticity and excellent machinability, to create durable and optically clear plastic parts. Finishing options for polycarbonate machined parts include polishing or coating to enhance surface quality and appearance.
The best cutting tools for polycarbonate are CNC cutters or circular saws designed for engineering plastics, offering precision and durability. These tools are essential for achieving smooth cuts on plastic sheet machining projects and for creating large parts or detailed polycarbonate machined parts. Whether for CNC milling, CNC turning, or other machining methods, selecting the right tools ensures quality results and preserves the excellent impact strength and machinability of the material.
CNC Resources

What is Steel | Definition, Properties, and Composition Explained
Steel is an alloy that is primarily composed of iron and carbon, and it’s the world’s most widely used material.

Bronze vs. Copper: Key Differences, Uses, and Benefits
The main difference between bronze and copper is in their different composition — copper is a pure metal, whereas bronze

Bronze vs. Brass: Key Differences, Uses, and Which to Choose
The main difference between bronze and brass lies in their composition: bronze is an alloy primarily composed of copper and
Start today. Get parts made fast.
Free Machined Parts Design to Your Projects with Fast Turnaround Times.